Table of contents
In the ever-evolving world of manufacturing, efficiency and precision are paramount. As industries strive for perfection, the role of advanced machinery like CNC lathes and precision milling tools becomes increasingly significant. This blog post explores how leveraging rebuilt CNC lathes and state-of-the-art milling tools can substantially enhance productivity, offering insights into the transformation of raw materials into intricate components with unrivaled accuracy. Read on to uncover the potential benefits and understand the impact of these technological advancements on your production line.
Revitalizing Production with Rebuilt CNC Lathes
Introducing rebuilt CNC lathes into a manufacturing setup affords a plethora of advantages, particularly from a financial perspective. Opting for CNC lathe refurbishment is a strategic move that can lead to substantial cost savings, a factor that inevitably resonates with budget-conscious production managers. Instead of allocating resources for the acquisition of brand-new equipment, businesses can invest in retrofitting existing machinery. This approach not only conserves capital but also aligns with sustainable production practices by extending the service life of tools and reducing waste.
Beyond the immediate monetary benefits, reconditioned CNC lathes embody advanced manufacturing technology, ensuring that industries remain competitive with precision machining capabilities. The environmental footprint of manufacturing operations is also considerably diminished, as the need to produce and transport new machines is curtailed, exemplifying responsible resource management and adherence to emerging ecological standards. In essence, the integration of expertly rebuilt CNC systems supports a cost-effective manufacturing paradigm, without compromising on the high-performance demands of modern production environments.
Maintaining Precision with High-Quality Milling Tools
The importance of utilizing high-quality milling tools cannot be overstated when it comes to precision manufacturing. These tools are pivotal in ensuring the dimensional accuracy required in intricate production tasks. By using the right milling tools, manufacturers can achieve tighter tolerances that are indispensable for components to fit together perfectly in complex assemblies. Moreover, a superior surface finish, which is a direct result of the refined quality of milling tools, plays a significant role in enhancing the end product's aesthetic and functional attributes. This focus on milling tool quality not only elevates the standard of the finished goods but also bolsters industrial productivity by minimizing the need for additional finishing processes. Entities such as SAMO Machine Tools exemplify the commitment to tooling excellence, offering solutions that cater to these high standards of manufacturing. For those in the industry, it's clear that the choice of tools directly correlates with the success of production outcomes, making the selection of top-tier milling equipment an investment in both quality and efficiency.
Upgrading Efficiency with Advanced Control Systems
Modern control systems embedded within rebuilt computer numerical control (CNC) lathes and precision milling tools are transformative in efficiency enhancement, enabling machines to operate with greater precision and speed. By incorporating advanced control systems, manufacturers can significantly reduce waste and improve the speed of production. The integration of up-to-date software with the hardware components is pivotal for the optimization of machine performance. It allows for real-time monitoring and adjustments, ensuring that machining processes are not only efficient but also consistent in quality. Consequently, this technological synergy between advanced control systems and rebuilt CNC machinery underpins a more streamlined production process, leading to increased overall profitability and a reduction in materials and time expenditure. These benefits emphasize the significance of software integration in realizing the full potential of efficient machining capabilities.
Extending Equipment Life and Reducing Downtime
In the realm of manufacturing, equipment longevity and minimized downtime are vital factors that significantly enhance productivity. Rebuilt CNC lathes and precision milling tools are at the forefront of reliable manufacturing solutions, offering a second life to machinery that might otherwise be considered for replacement. Implementing a regimen of preventative maintenance is the cornerstone of maintaining these high-precision tools, ensuring they operate at peak performance for extended periods. This practice not only extends the functional lifespan of the equipment but also plays a pivotal role in the reduction of operational costs. Consistent upkeep and timely interventions prevent the occurrence of unforeseen breakdowns that can halt production, leading to costly delays. Through maintenance best practices, businesses can ensure that their CNC machinery remains a robust asset, rather than a liability, thereby maintaining a steady and efficient production line.
Maximizing Return on Investment with Rebuilt Machines
For manufacturers looking to optimize their financial outlay, investing in rebuilt CNC lathes and precision milling tools represents a savvy cost-saving strategy. Rebuilt machinery value hinges on the lower initial costs compared to brand-new equipment—an appealing factor that directly impacts the total cost of ownership (TCO) positively. By acquiring these reconstructed machines, manufacturing entities can significantly reduce capital expenditure, redirecting funds into other avenues of their business that may need attention or expansion.
Moreover, the integration of rebuilt CNC lathes and precision milling tools into a production line does not mean a compromise on efficiency or capability. These machines are meticulously restored to meet stringent industry standards, often boasting enhancements that lead to high-efficiency production. Investment maximization is further achieved as these tools can elevate output quality and speed, contributing to increased productivity levels. This blend of affordability, superior performance, and extended equipment lifespan establishes rebuilt machinery as a cornerstone for driving a higher return on investment for discerning manufacturers.
Similar
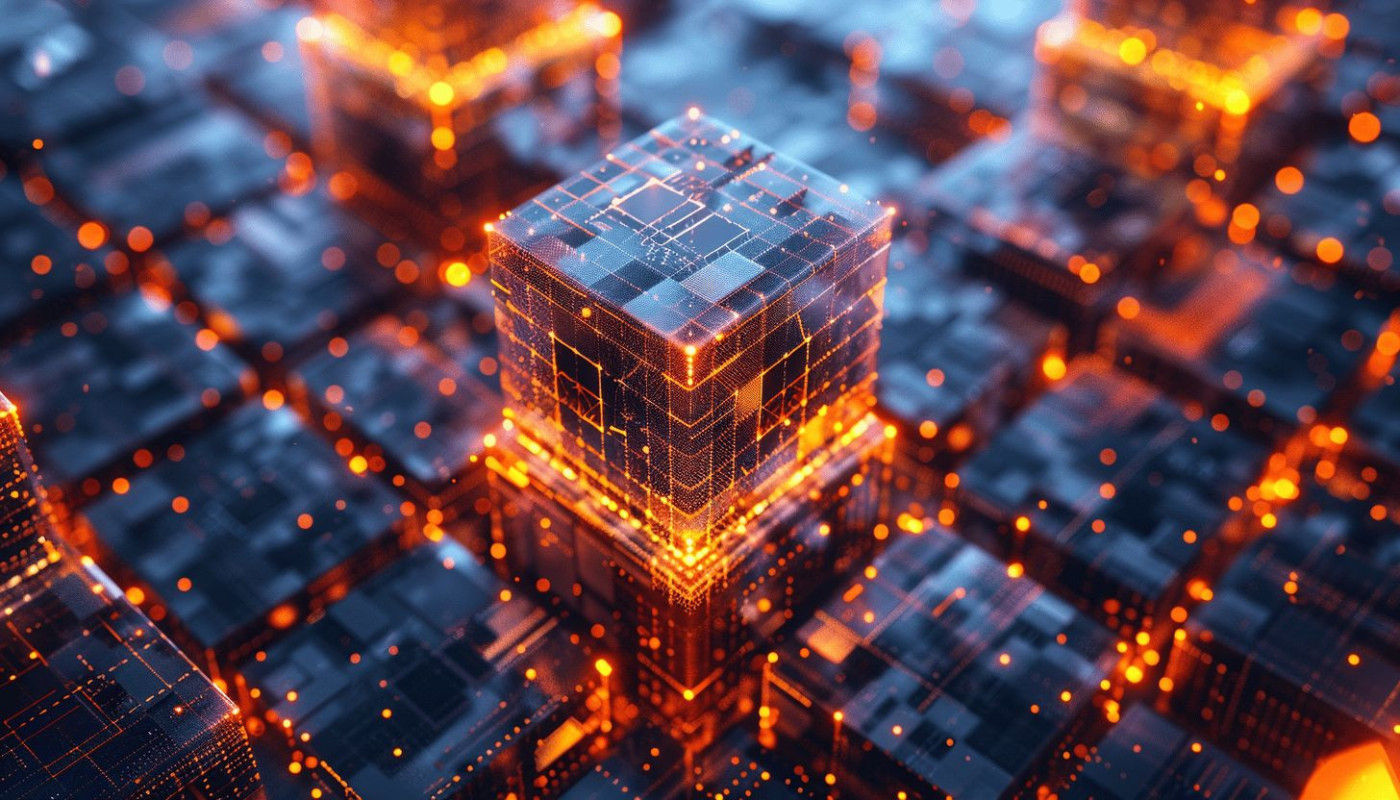
The impact of blockchain technology on financial transactions in business
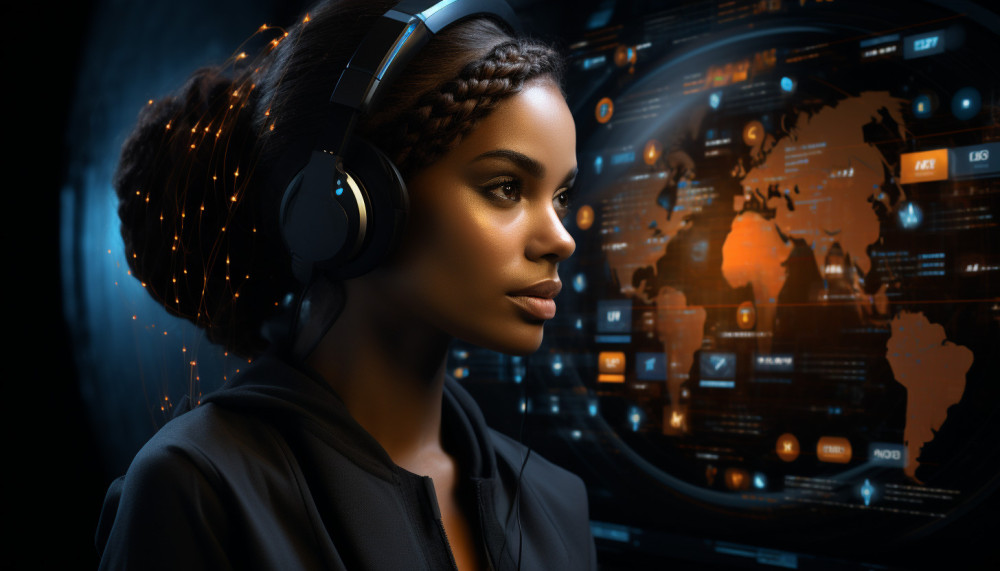
Maximizing Productivity: Strategies For Implementing Automated Dialing In Outbound Call Centers
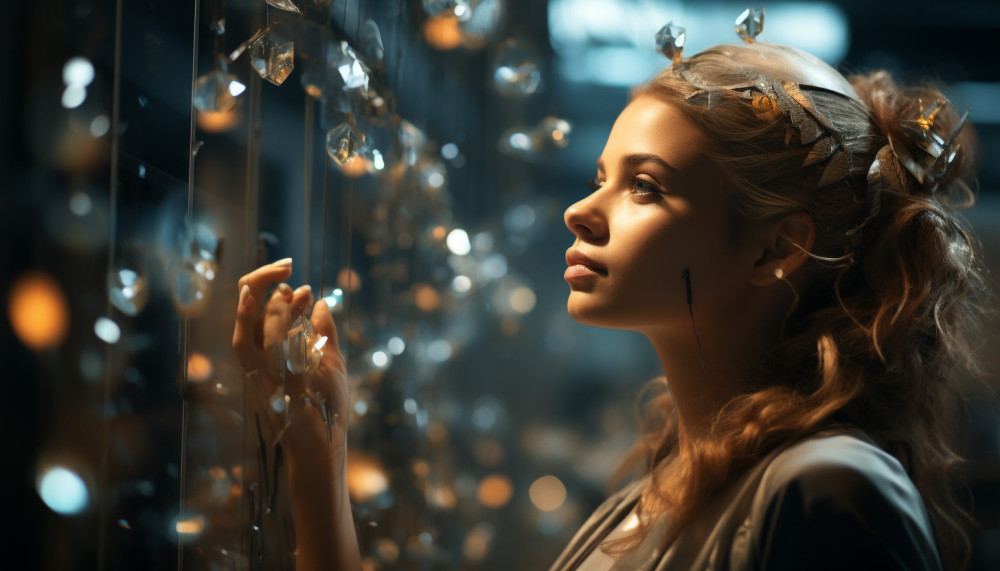
How AI Is Shaping The Future Of Job Roles In The Translation Industry
